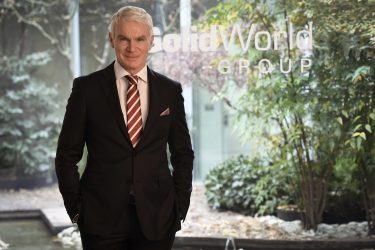
Roberto Rizzo (SolidWorld): «Dai software alle stampanti 3D, trasformiamo le aziende in fabbriche digitali»
A Treviso c’è un angolo di rivoluzione digitale in corso. SolidWorld, fondata nel 2003 da un ingegnere aeronautico, Roberto Rizzo, accompagna le aziende nella transizione verso la «fabbrica digitale», dalla A alla Z: fornendo software ma anche hardware – a partire dalle stampanti 3D – e formazione, oltre che realizzando parte della produzione per i clienti. A capo di un gruppo con un fatturato che al 30 giugno 2021 era pari a 28,9 milioni di euro, in crescita del 29% rispetto a un anno prima, con oltre 150 dipendenti e più di 8mila imprese clienti, Roberto Rizzo (presidente e Ad di SolidWorld) ha un punto di vista privilegiato sul futuro della manifattura italiana. Dove l’accorciamento delle catene di fornitura provocato dallo choc della pandemia ha accelerato l’adozione di tecnologie «intelligenti».
Rizzo, che cosa lega l’aeronautica alle “fabbriche digitali”?
Mentre scrivevo la tesi in ingegneria aeronautica andai negli Stati Uniti e lì vidi, erano gli anni Ottanta, per la prima volta la tecnologia Cad applicata alla progettazione degli aerei Boeing. Ho pensato che quello sarebbe stato il mio futuro e, una volta tornato in Italia, ho fondato la mia prima società che si occupava di tecnologia 3D per settori quali componenti auto e sport system. Dopo 15 anni ho ceduto quella società è ho dato vita a SolidWorld, che utilizza tecnologie proprie integrando software importati dall’estero. Negli anni ho acquisito altre aziende per completare l’offerta affiancando al software la parte hardware. Siamo stati tra i primi a fornire stampanti tridimensionali per l’industria, integrandole con la progettazione. Oggi SolidWorld Group conta 12 aziende in tutta Italia, di cui tre sono poli tecnologici, ovvero vere e proprie fabbriche digitali che producono per i nostri clienti. Curiamo tutta la filiera dalla progettazione di un nuovo prodotto alla realizzazione degli esecutivi, fino al collegamento con i software ERP.
Qual è la sua definizione di fabbrica digitale e davvero è alla portata delle piccole-medie imprese italiane?
Oggi l’azienda è fatta di tante isole di lavoro: c’è iper-connessione tra tutti ambienti, dalla produzione alla progettazione, dalla logistica al delivery. Industry 4.0 non è altro che connettività: software connessi per controllare tutto il processo, facendo comunicare tra loro tutte le fasi produttive. L’Italia è la seconda manifattura d’Europa ma, rispetto a Germania, non operiamo per grandi volumi. Le nostre fabbriche sono estremamente flessibili, design e funzionalità sono la forza dei loro prodotti. Grazie alle tecnologie 4.0 queste aziende hanno la possibilità di riprogrammare velocemente l’attività di ogni isola in funzione delle esigenze del cliente.
Quanto ha influito la pandemia su questa transizione?
Con le incertezze sulle forniture dall’estero dovute alla pandemia e con l’incremento dei costi dei trasporti sta diventando antieconomico, per chi realizza prodotti di qualità elevata, delegare all’estero, magari in Cina o in Vietnam, parti della produzione. Le catene di fornitura globali si sono dimostrate fragili e i processi di reshoring sono complementari all’adozione di processi di fabbrica intelligente.
Qualche esempio?
Tra i nostri clienti c’è lo storico marchio di biciclette Bianchi, che ha dichiarato che tornerà a produrre tutto in Italia. Un altro cliente realizza vasche da bagno di altissima qualità, e la fabbrica intelligente permette loro di coniugare due esigenze: la perfezione del prodotto e i tempi di consegna molto ridotti. Ma tra i nostri clienti c’è anche Fca per i suoi stabilimenti italani, che oggi sono strutture d’eccellenza, e infatti in Italia Fca produce le 500, che sono quasi un oggetto di design. Ma questa trasformazione riflette anche un cambiamento sociale del modo di intendere il lavoro.
In che senso?
I tecnici specializzati sono sempre più difficili da trovare, e anche per questo noi partecipiamo agli ITS, gli istituti che li formano. Siamo indirizzati verso una società signorile di massa, per citare la formula di Luca Ricolfi, anche l’operaio vuole avere un lavoro “pulito”. La fabbrica digitale dà questa possibilità, grazie ai cobot: è pulita, silenziosa, lavora 24 ore su 24 senza bisogno dei turni di notte, grazie al controllo da remoto delle operazioni. La nostra tecnologia risponde a questa doppia esigenza: di mercato, la velocità di risposta a un cliente sofisticatoo, e sociale, l’adattamento alle nuove esigenze delle persone.
Dieci anni fa la stampante 3D veniva raccontata come il futuro, per poi sparire dai radar. Cos’è cambiato oggi?
All’epoca si leggeva che tutti ne avrebbero avuta una in casa. Ma per utilizzarla non bastava l’hardware, serviva un software di modellazione 3D che solo le industrie possono permettersi. Oggi servono a fare due cose: da un lato i prototipi di nuovi prodotti, dall’altro la produzione vera e propria, che nell’ultimo anno sta prendendo sempre più piede, grazie a stampanti di nuova generazione in grado di stampare sia in polimero che in acciaio in tempi sempre più rapidi. Rispetto a due anni fa, grazie all’utilizzo di nuovi motori, riusciamo a stampare in un terzo del tempo. Una stampante professionale può produrre integralmente il telaio di una bicicletta. Elimina la necessità di fare gli stampi, che costano energia e tempo. Se poi si installano pannelli solari sui tetti del capannone, si riescono a stampare lotti medio-piccoli in modo sostenibile. Nelle nostre tre fabbriche digitali in estate non spendiamo un euro in energia, grazie agli impianti solari.
Quali sono i vostri principali settori di attività?
Aerospaziale, automotive, macchine automatiche, home design, cantieristica navale, solare ed eolico. Alcuni nostri clienti stanno progettando le piattaforme eoliche offshore al largo delle coste italiane. Recentemente ci siamo aperti al settore biomedicale, sviluppando un software di trasformazione di risonanze magnetiche e tomografie assiali in modelli digitali tridimensionali. Aiutiamo i chirurghi stampando in 3D un modello digitale dell’organo malato da operare, affinché si possano esercitare nel caso di operazioni particolarmente complesse.
Che ruolo giocano i programmi governativi e i fondi del PNRR per guidare la trasformazione digitale dell’industria?
Il Superbonus 110% ha dato la spinta al rinnovamento del parco edilizio aprendo la strada al risparmio energetico, ora speriamo che il PNRR porti un simile ammodernamento al sistema industriale, per renderlo competitivo, flessibile e veloce e proseguendo sulla giusta strada iniziata con le agevolazioni Industria 4.0 nel 2017. I fattori strategici su cui intervenire nelle aziende sono due: da un lato massima velocità di risposta ai cambiamenti del mercato e delle esigenze del cliente, dall’altro architetture aperte con altri sistemi. Servono investimenti molto importanti, le tecnologie sono molto costose ma non c’è alternativa.
Giulio Todescan